At the forefront of surface treatment technologies, nitriding sandblasting has emerged as a key innovation, changing the landscape of traditional sandblasting methods. This advanced technique incorporates nitrogen into the abrasive stream, revolutionizing the way surfaces are cleaned, prepared, and finished. In this article, we will delve into the nuances of nitriding sandblasting, explore its unique advantages, and investigate the diverse applications that make it a game-changer in industries seeking precision, safety, and superior surface quality.
1. What is Sandblasting nitriding?
Sandblasting nitriding is an advanced surface treatment technique that integrates traditional sandblasting with nitriding into the abrasive stream. In conventional sandblasting, abrasive materials, like sand, are propelled at high velocity to clean the surface. The incorporation of nitrogen into this process brings about several important improvements and benefits.
Nitrogen gas is introduced into the abrasive stream through specialized equipment, enabling precise and controlled integration. This modification imparts distinctive characteristics to the sandblasting process, influencing its impact on the surface in ways unattainable with traditional methods.
2. Sandblasting nitriding process
Combining sandblasting with nitriding can be a strategic approach in specific applications, particularly those involving products with stringent surface requirements. This process typically encompasses the following steps:
2.1. Step 1: Prepare the surface
- Inspect the material surface for contaminants, rust, residue, or old coatings.
- Determine the specific surface roughness and cleanliness requirements for the intended application.
2.2. Step 2: Abrasive selection and equipment setup
- Select the appropriate abrasive media (for example, sand, glass beads, aluminum oxide) based on the material and the desired surface properties.
- Install sandblasting equipment, including the blast chamber or cabinet, air compressor, and nozzle.
- Load the selected abrasive into the hopper of the blast chamber.
2.3. Step 3: Sandblasting process
- Place the material into the chamber, ensuring that it is securely positioned.
- Commence the sandblasting process, utilizing compressed air to propel abrasive particles through the nozzle onto the material’s surface.
- Fine-tune blasting parameters such as pressure, angle, and distance to achieve the desired surface roughness.
2.4. Step 4: Clean the surface
- After sandblasting, clean the material thoroughly to eliminate any lingering abrasive particles and debris.
- Inspect the surface to verify that it adheres to the specified cleanliness and roughness standards.
2.5. Step 5: Preheat
- Preheat the material to be sandblasted in a controlled environment, typically one with an ammonia-rich or dissociated ammonia atmosphere.
- Ensure that the material reaches the appropriate temperature for nitrogen diffusion.
2.6. Step 6: Nitriding
Expose the material to a nitrogen-rich environment for a predetermined period, enabling the nitrogen to diffuse into the surface. Monitor and control the nitriding temperature and time to achieve the desired case depth.
2.7. Step 7: Cool
Gradually cool the material to preserve the nitriding-induced layer, and carefully control the cooling rate to prevent deformation or cracking.
2.8. Step 8: Post-nitriding treatment (if any)
Depending on the application, conduct additional treatments, such as quenching or annealing, to further refine the properties of the material.
2.9. Step 9: Quality control
Test materials for the desired surface properties, including hardness, microstructure, and overall quality.
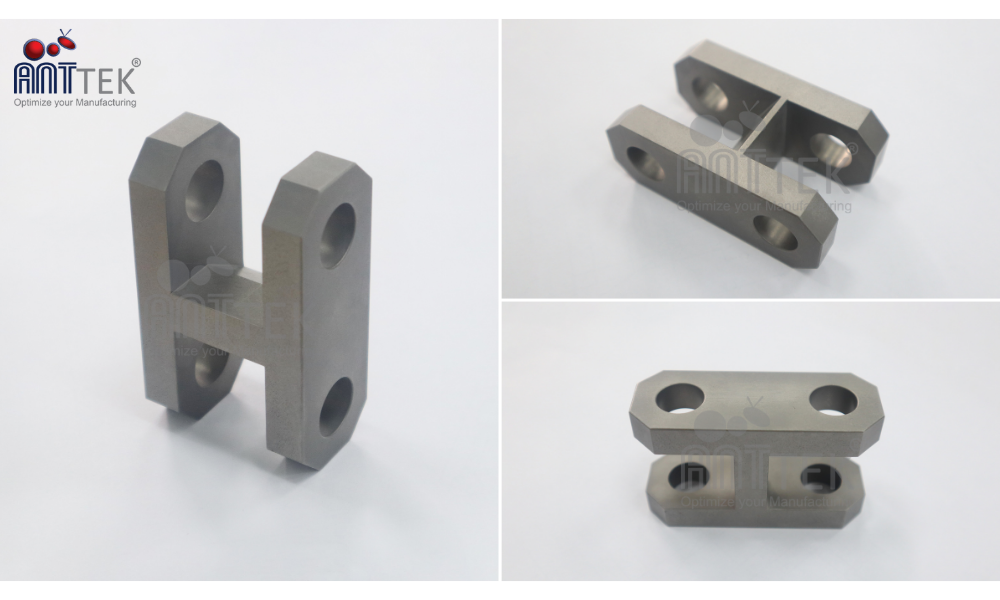
3. Benefits of Sandblasting nitriding
3.1. Surface Cleaning
Sandblasting eliminates contaminants, oxides, and surface irregularities, yielding a clean and textured surface. The roughened texture enhances the nitriding process by offering additional reaction sites for nitrogen diffusion, leading to a more uniform and deeper case hardness.
3.2. Enhancing the adhesion of the nitrogen layer
Sandblasting facilitates a strong mechanical bond between the substrate and the nitriding layer. Improved adhesion ensures that the nitrided layer tightly adheres to the material, reducing the risk of peeling or delamination over time.
3.3. Controlled surface finish
Sandblasting enables precise control over surface finish, allowing for the attainment of a specific roughness or texture as desired. When combined with nitriding, manufacturers can achieve an optimal surface finish that serves both functional and aesthetic purposes.
3.4. Enhanced abrasion resistance
Nitriding enhances surface hardness, wear resistance, and corrosion resistance. When combined with sandblasting, it ensures excellent adhesion of the nitriding layer to the surface, thereby maximizing the benefits of improved mechanical and chemical properties.
3.5. Consistent nitriding
The uniformly prepared surface achieved through sandblasting promotes even nitrogen diffusion during the nitriding process. This uniformity ensures consistent hardness and mechanical properties across the treated material, thereby minimizing the risk of localized weaknesses.
3.6. Extends component life and performance
The synergistic effects of sandblasting and nitriding contribute to the extended service life of parts, particularly in applications with high wear, fatigue, or corrosive conditions. Enhanced hardness and wear resistance not only reduce maintenance needs but also increase reliability.
4. Anttek Viet Nam – Sandblasting nitriding service manufacturer and supplier
Anttek Vietnam is proud to be a leading designer and fabricator of machine parts, delivering high-quality and reliable products to our customers. We have been supplying every machining service from giving advice, designing, machining to heat treatment, surface treatment such as white/black anodizing, electroless nickel plating, sandblasting nitriding…
With many years of experience in jig design and processing, Anttek Vietnam has been a trusted partner for both domestic and international clients.
For details, please contact:
—————————
ANTTEK VIET NAM – SPECIALIZING IN PRECISION MECHANICAL MACHINING
Headquarters: Lot G07, Kien Hung Land QSD Auction, Kien Hung Ward, Ha Dong District, Hanoi City, Viet Nam
Factory: Lot 6, Lai Xa Industrial Cluster, Kim Chung Commune, Hoai Duc District, Ha Noi City, Viet Nam.
Hotline: (+84) 988 688 336 / (+84) 385 552 628
Email: khoi.pd@anttekvietnam.com
Website: https://anttekvietnam.com
The combination of nitriding and sandblasting provides a comprehensive approach to surface treatment, offering synergistic benefits that enhance material properties and performance. This process is commonly employed in industries where parts are exposed to demanding conditions, requiring improved wear resistance.