In the realm of precision mechanical machining, where every micron counts, the smallest details can make a significant difference in the quality and functionality of the final product. One such crucial detail is chamfering, a process that not only enhances the aesthetics of a component but also plays a vital role in functionality, particularly in parts where sharp edges can lead to stress concentrations or assembly difficulties. Among various chamfering techniques, C chamfering stands out as a specialized method with distinct advantages in precision machining.
What is C Chamfering?
C chamfering, also known as circular chamfering or contour chamfering, is a technique employed in precision machining to create a chamfer with a circular profile along the edges of a workpiece. Unlike conventional chamfering, which typically results in a straight or angled edge, C chamfering involves the creation of a smooth, rounded contour, resembling the shape of the letter ‘C’. This rounded profile offers several benefits over traditional chamfering methods, making it particularly well-suited for applications where precision, aesthetics, and functionality are paramount.
Chamfer errors in precision mechanical machining
Inconsistent Chamfer Size
- Cause: Uneven feed rates or tool deflection.
- Solution: Ensure consistent feed rates and use rigid tooling to minimize deflection.
Chamfer Angle Inaccuracy
- Cause: Incorrect tool geometry or misalignment of the workpiece.
- Solution: Use appropriate tool geometry and ensure proper setup and alignment of the workpiece.
Rough or Uneven Chamfer Surface
- Cause: Inadequate tool sharpness, incorrect cutting parameters, or poor toolpath strategies.
- Solution: Use sharp tools, optimize cutting parameters, and improve toolpath programming.
Chamfer Edge Breakage
- Cause: Excessive cutting forces, improper tool selection, or incorrect cutting speeds and feeds.
- Solution: Adjust cutting parameters, select a more suitable tool material or geometry, and use coolant/lubrication to reduce cutting forces.
Mismatched Chamfer Dimensions
- Cause: Inaccurate tool setup, worn-out tools, or machine calibration issues.
- Solution: Check and adjust tool setup, replace worn-out tools, and calibrate the machine regularly.
Chamfer Overcut or Undercut
- Cause: Improper toolpath programming, tool deflection, or inaccurate machine positioning.
- Solution: Optimize toolpath strategies, use rigid tooling, and ensure precise machine positioning.
C chamfering techniques in precision mechanical machining
CNC Machining
CNC machining is one of the most widely used techniques for C chamfering in precision mechanical machining. CNC machines offer precise control over cutting tools, allowing for the creation of intricate chamfer profiles with high accuracy and repeatability. Multi-axis CNC machining centers equipped with advanced tooling capabilities enable machinists to achieve complex C chamfers on various workpiece geometries.
End Milling
End milling is a common technique employed in C chamfering, particularly for creating chamfers on flat surfaces or along the edges of a workpiece. End mills with specially designed profiles, such as bullnose or radius end mills, are utilized to generate the desired rounded contours. By controlling the depth of cut and the feed rate, machinists can achieve precise C chamfers with smooth surface finishes.
Corner Rounding
Corner rounding is another technique used in C chamfering, primarily for rounding the sharp corners of a workpiece. Specialized corner rounding tools, such as radius cutters or corner rounding end mills, are employed to remove material gradually and create a smooth transition from the flat surface to the curved edge. This technique is particularly useful for applications where sharp corners need to be avoided to reduce stress concentrations or improve aesthetics.
Abrasive Finishing
Abrasive finishing techniques, such as grinding or sanding, are sometimes employed in C chamfering to achieve fine surface finishes and precise edge profiles. Abrasive wheels or belts with contoured shapes are used to remove material gradually and create smooth, rounded chamfers. This technique is often utilized in conjunction with CNC machining to refine the chamfered edges and achieve tight tolerances.
Advantages of C Chamfering
Improved Aesthetics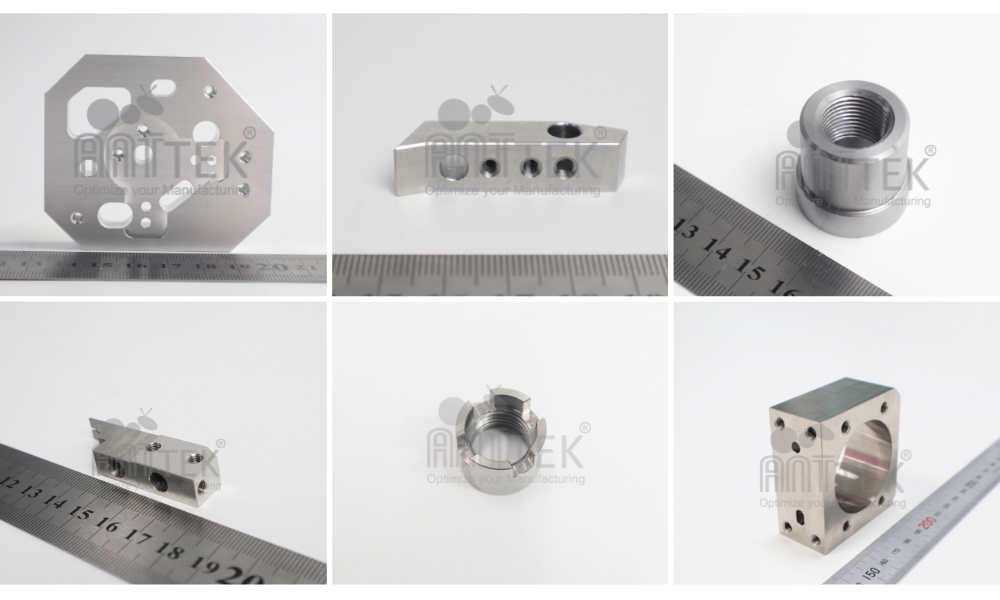
In precision engineering, aesthetics play a crucial role, particularly in components intended for consumer products or high-end machinery. The smooth, rounded edges produced by C chamfering not only enhance the visual appeal of the finished product but also convey a sense of quality and craftsmanship. Whether it’s a meticulously machined gear or a finely crafted housing, the attention to detail afforded by C chamfering can elevate the perceived value of the final assembly.
Enhanced Functionality
Beyond aesthetics, C chamfering can also enhance the functionality of machined components. In applications where parts need to fit together precisely or undergo assembly processes, sharp edges can pose challenges, leading to difficulties in alignment or potential damage during handling. The rounded profile created by C chamfering facilitates smoother assembly, reduces the risk of damage, and ensures optimal performance of the finished product.
Versatility
While C chamfering is commonly associated with precision machining, its versatility makes it suitable for a wide range of materials and applications. Whether machining metal alloys, engineering plastics, or composite materials, C chamfering can be adapted to suit different material properties and machining requirements. This versatility makes it a preferred choice for industries ranging from aerospace and automotive to electronics and medical devices.
C chamfering techniques in precision mechanical machining encompass a range of methods tailored to create smooth, rounded contours along the edges of machined components. From CNC machining and end milling to corner rounding and abrasive finishing, each technique offers unique advantages in terms of accuracy, surface finish, and versatility. By leveraging these techniques effectively, machinists can produce high-quality components with precisely chamfered edges, meeting the stringent requirements of various industries, including aerospace, automotive, electronics, and medical devices.