Precision machining plays a key role in manufacturing industries, ensuring the creation of complex and precise parts for various applications. Nevertheless, even with advanced technologies and meticulous processes, shape deviations can still occur, potentially impacting the quality and functionality of the final product.
1. Types of shape deviations in precision mechanical processing
The classification of product shape deviations in precision machining is crucial for comprehending and addressing the various problems that may arise.
1.1. Flatness deviation
Flatness deviation is a geometric irregularity that pertains to variations in the flatness of a surface. In precision machining, obtaining and preserving flatness is crucial, particularly for parts with stringent tolerances. The measurement of flatness deviation involves comparing the actual surface profile with the theoretically perfect surface profile.
1.2. Straightness deviation
Straightness deviation is a geometric parameter that signifies the deviation of a linear feature from a perfectly straight line. In precision machining, achieving and maintaining straightness is crucial for components where linear alignment is a critical requirement.
1.3. Cylindricity deviation
Cylindricity deviation pertains to variations in the shape and alignment of a cylindrical feature from its intended specifications in precision mechanical machining. Cylindrical features are prevalent in many mechanical parts, such as shafts, pins, and bearings. Achieving and maintaining the correct cylindrical shape is essential to ensure the proper functioning of a larger mechanical system.
1.4. Roundness deviation
Roundness deviation is a crucial aspect of precision machining, referring to the alteration in the roundness of cylindrical features. Achieving and maintaining roundness is particularly essential in components like bearings, shafts, and other rotating parts, where even slight misalignments can impact performance.
1.5. Profile Deviation
Profile deviation refers to a change in the shape or contour of an object along its longitudinal axis. In precision machining, maintaining the desired longitudinal profile is crucial for components such as shafts, rails, or beams. Deviations from the intended configuration can significantly impact the functionality and performance of the part.
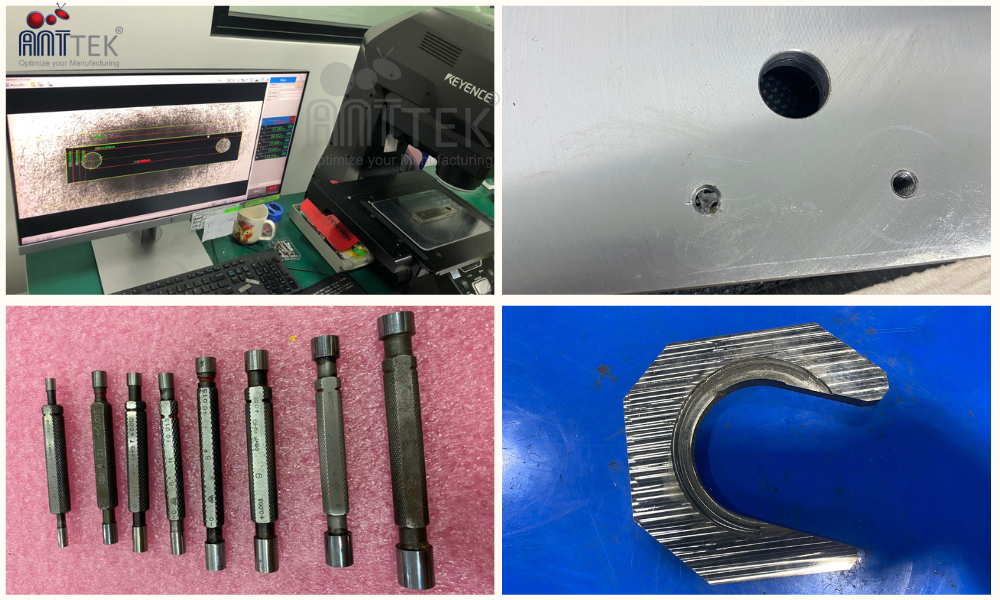
2. Causes of shape deviations
2.1. Worn-out and broken tools
One of the main causes of shape deviation is tool wear or breakage during machining. When cutting tools interact with the workpiece, they gradually wear out, affecting machining accuracy. On the other hand, breakage can result in sudden changes during machining, leading to undesired shape variations.
2.2. Material inconsistency
Materials utilized in precision machining may exhibit inherent variations in properties, such as hardness and composition. These inconsistencies can result in uneven material removal, leading to shape distortions. Proper material testing and selection are crucial to minimize such variations.
2.3. Programming error
The machining process is frequently governed by computer numerical control (CNC) programs. Errors in the programming phase, such as inaccuracies in toolpaths or feed rates, can result in shape deviations. Comprehensive testing and simulation before the actual machining can assist in identifying and rectifying such issues.
3. How to minimize shape deviations in precision mechanical machining
3.1. Check and replace tools regularly
Implementing a proactive tool maintenance strategy is crucial for minimizing tool wear and breakage. Regular inspection and timely replacement of worn or damaged tools can significantly reduce the likelihood of shape deviations.
3.2. Material quality control
Strict adherence to material quality standards and thorough testing can aid in identifying and resolving material inconsistencies. Collaborating closely with material suppliers and conducting internal quality tests are essential steps to ensure consistent material properties.
3.3. Equipment Calibration
Regularly calibrating machining equipment and employing damping techniques can help minimize the influence of machine dynamics on shape deviations. Ensuring that machinery is in optimal condition and free of vibrations is essential for precision machining.
3.4. Programming
Investing time in CNC programming and conducting thorough simulations before actual machining can help identify and correct programming errors. This process involves confirming toolpaths, feed rates, and other parameters to ensure accurate and consistent machining.
For details, please contact:
—————————
ANTTEK VIET NAM – SPECIALIZING IN PRECISION MECHANICAL MACHINING
- Headquarters: Lot G07, Kien Hung Land QSD Auction, Kien Hung Ward, Ha Dong District, Hanoi City, Viet Nam
- Factory: Lot 6, Lai Xa Industrial Cluster, Kim Chung Commune, Hoai Duc District, Ha Noi City, Viet Nam.
- Hotline: (+84) 988 688 336 / (+84) 385 552 628
- Email: khoi.pd@anttekvietnam.com
- Website: https://anttekvietnam.com
Attaining precision in machining is a complex process that demands meticulous attention to detail at every stage. By comprehending the typical causes of shape deviations and implementing effective mitigation solutions, manufacturers can enhance the quality and reliability of precision machined parts. Continuous improvement, regular maintenance, and a steadfast commitment to quality control are crucial and decisive factors in the pursuit of precision in the field of mechanical machining.